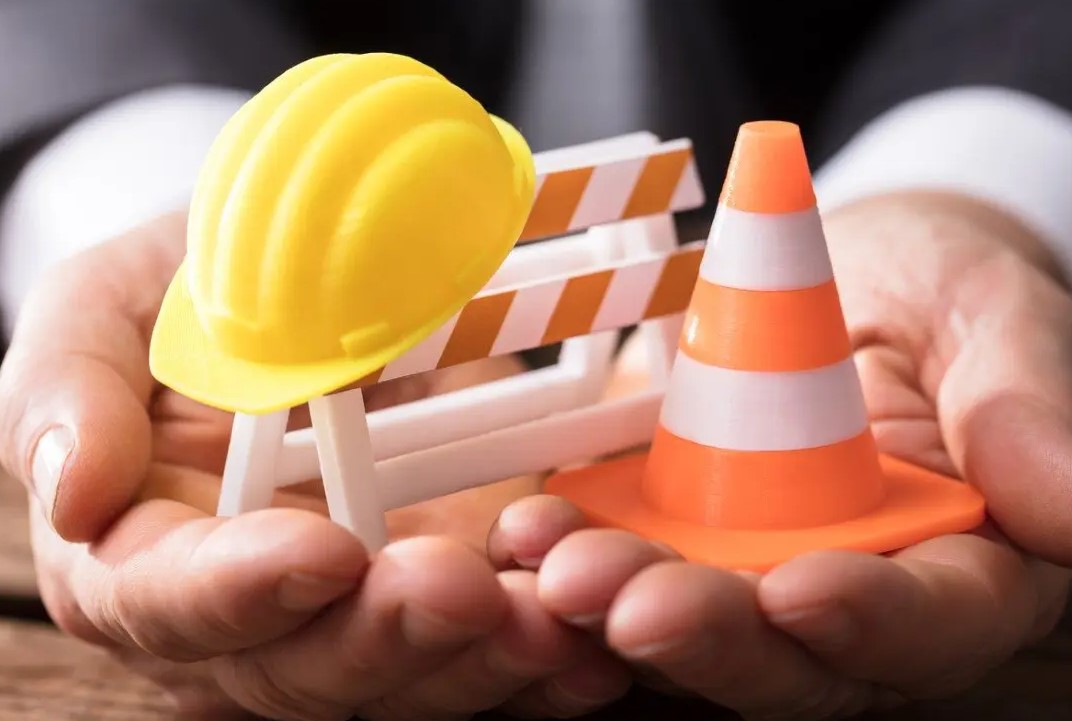
In recent years there has been a lot of attention towards healthy and safe workplace environments across all industries. No matter the line of work a company is in, there need to be some laws and regulations involved that are there to protect the employers as well as the reputation of the whole operation.
Workers are harder and harder to come by for many reasons, especially in highly specialized industries that take years of experience to master. This is particularly true for companies that deal in any and all forms of manufacturing.
The use of dangerous machinery that can seriously hurt or even kill its operator if they lack proper training is an everyday occasion in any company that manufacturers goods. It hardly matters how big or small the final product is.
There are always countless of ways in which an unsuspecting employee can get hurt and have lifelong consequences because of it. This is why workplace safety is of the utmost importance in the 21st century. We know more, we are informed better, so we also have to do different things than our predecessors.
In this article we talk about the overall importance of workplace safety in terms of manufacturing companies. If you run such a company, work in one, or simply want to know more about this ever-important topic, keep reading this article. What is more, be sure to check out this website in case there are other things related to workplace safety you wish to continue learning.
Basic Overview
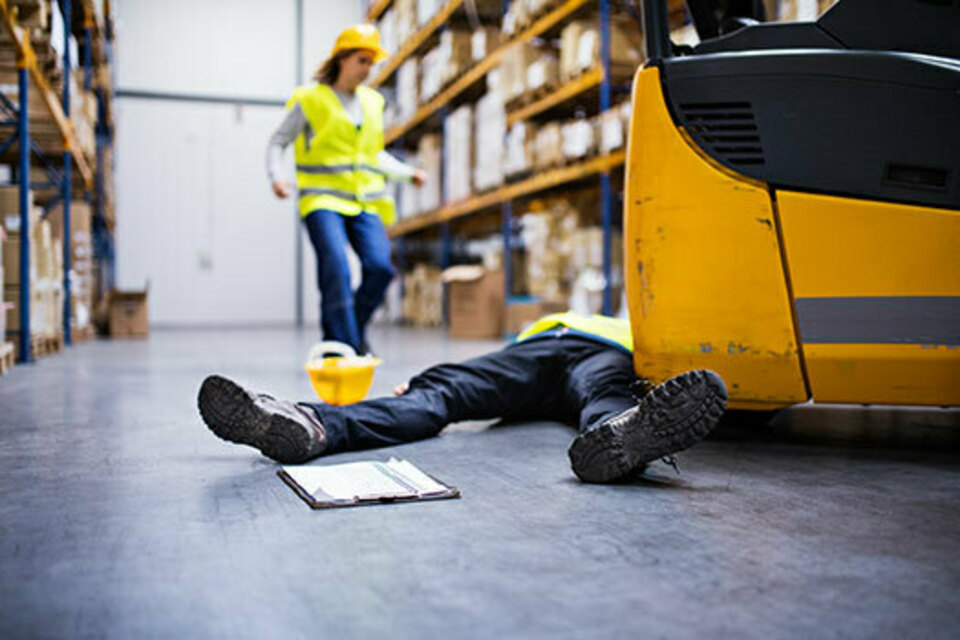
It is not rocket science really, but a common and easy to understand thing. Manufacturing safety is crucial for any workplace that has it simply because it keeps the people safe, unharmed, and alive. Industrial accidents have had a huge impact on the society throughout history, and despite them occurring less and less there are still many examples each year where people needlessly suffer at work.
It is not only the matter of an accident or an injury, but also illnesses and poor conditions that damage the health of employees over time. A safe workplace for all the employees is something that should go without saying. Sadly, the reality of the situation is often disappointing which is why more education on this matter is needed.
People are More Perceptive
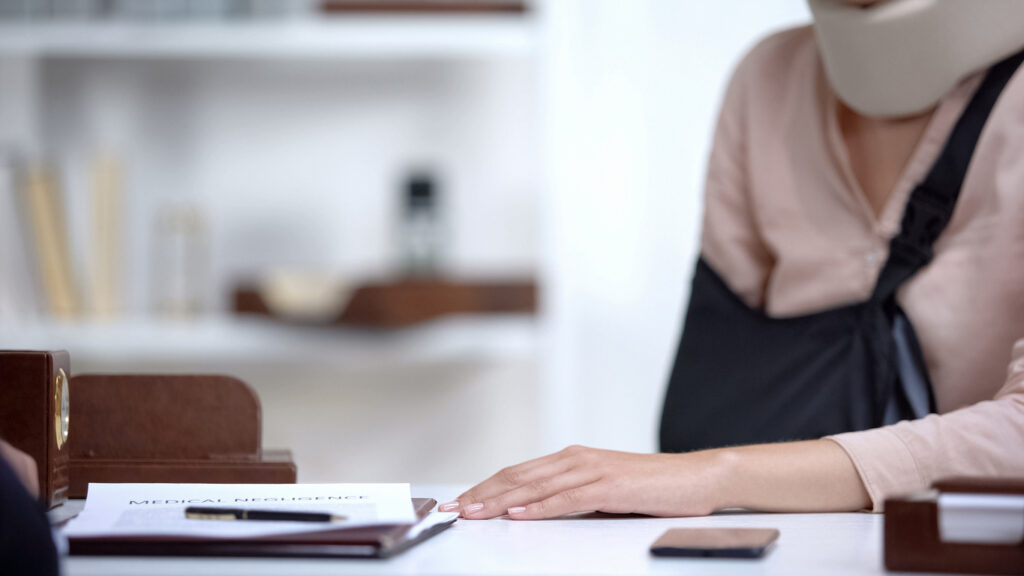
Of course, the workers know how dangerous their job is and they are fully aware of the dangers that come with working a certain job. This is however no reason for the employer to sit idly by as they struggle. It is up to the ownership and the management to provide the necessary measures and counter the issues at hand.
A modern employee knows his or her rights and they are able to recognize the responsibility of the higher-ups to keep them safe and protected while they work in their company and directly influence the steady streamline of revenue.
If there is ever a safety hazard or an issue of some sort, the need for everyone else to listen to the workers is crucial because they are the ones in danger after all. The problems start to arise and accumulate when other priorities get in the way and make those in charge preoccupied.
This whole topic then becomes the question of priorities and whether they have ever been in the right place. Trying to stay competitive on the market, run marketing campaigns, come up with new products and strategies, and remaining financially efficient are all concerns that come before general workplace safety in the manufacturing company.
The product they manufacture is often much more treasured and cherished that the people who make it or operate the machines that make it. Thing should actually be the other way around. As a result of this, safety becomes a drain on the resources and time of the company and those at the front lines suffer the consequences.
In the rush to hire and retain skilled workers, utilize new technologies, keep up with the laws, and constantly increase productivity, workplace safety falls lower and lower on the checklist. Soon, it is only a box that is checked without doing the work.
What Safety Measures Need to Exist?
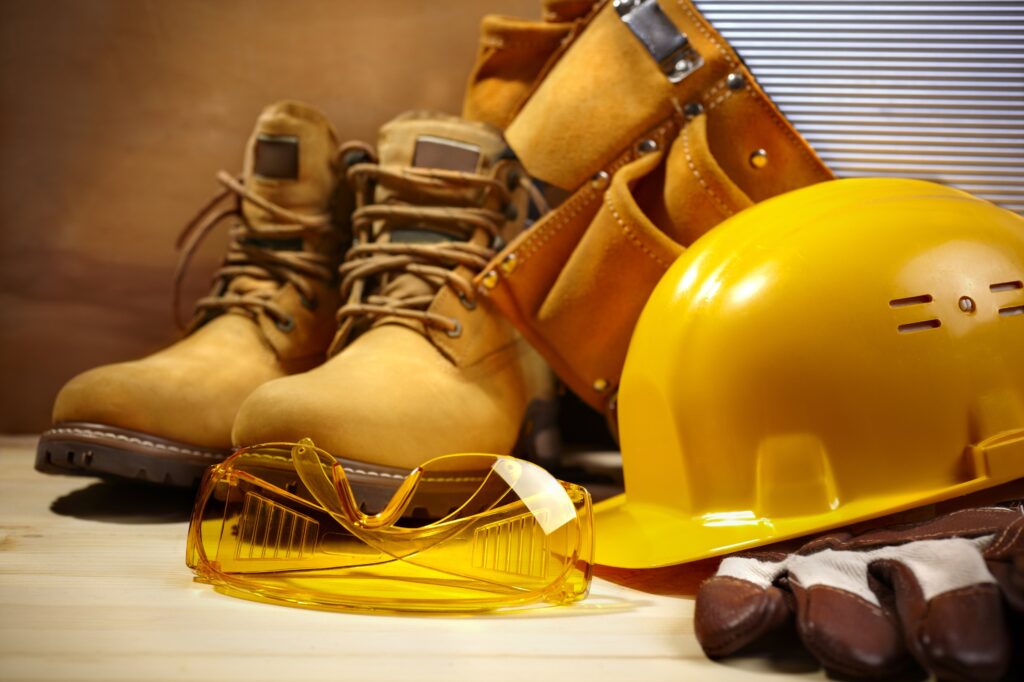
When you put it down on paper and start talking about it, things become quite clear and seemingly easy to follow. This is because they really are, but it can only be achieved if the higher-ups are on the same page.
It is all about the safety program a company has and the things it introduces into the workplace. Every manufacturing industry is different but they all have certain aspects in common. For a workplace to be as safe as it can, there needs to be extra attention put towards certain areas.
First of all, there needs to be a set of operating procedures and enough training for those operating dangerous machinery like lathes, presses, drills, saws, welding gear, cutting tools, and anything else that can seriously hurt or kill a person.
During operation and while on the premises, the right kind of goggles, gloves, boots, respirators, and helmets has to be worn by both the employees and the visitors. This is called personal protective equipment, or PPE for short, and the job should not be available for those refusing to comply. Wearing it is as important as checking it for malfunction and damage as well as maintaining its condition.
Are there any hazardous chemicals involved, and what is the best way to store them, handle them, and use them? Should anyone use them or just the certified personnel? Who is cleaning the workplace and who does the sanitization? In case of exposure, an accident like a fire or a leak, or a toxic substance being released, does everyone know what to do, how to behave, and where to go?
These are all aspects of workplace safety as a whole and they cannot be done poorly or in a rush. Health and safety training comes in many different ways and quite a few of its sides imply regular, yearly or even monthly refresher courses.
This all exists because the dangers are immense. Mitigating them with proper training and diligent behavior is the only way to protect yourself and the employee next to you, no matter the positions both people hold.