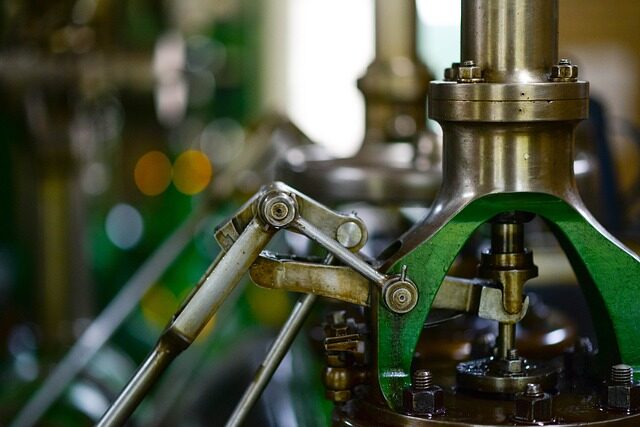
Metal stamping, an integral process in modern manufacturing, involves the use of dyes and punches to shape and deform metal into desired forms. From simple ornamental designs to intricate parts essential for machinery, metal stamping has facilitated the creation of a myriad of components that play a major role in our daily lives.
Tracing back its origins, metal stamps have been in existence for centuries, with artisans and manufacturers leveraging them for branding, design, and functional purposes. As industries evolved, so did the complexity and capabilities of metal stamping, turning it from a rudimentary hand tooling process to a sophisticated, automated operation.
This article aims to provide readers with a comprehensive understanding of how metal stamping underpins many facets of the manufacturing world, along with advancements in the metal stamping industry itself.
Metal Stamping Defined
Metal stamping is a manufacturing process that employs dyes and punches to deform and shape metal sheets into specific designs or parts.
This technique allows for the production of intricate and precise components on a large scale. There are various processes to create metal stamps, each tailored for different applications and outcomes.
For instance, blanking is used to cut out metal parts from a large sheet, piercing creates holes or slots in the metal, and forming shapes the metal into desired contours and geometries. Each process offers unique advantages depending on the final product’s requirements.
Advantages of Metal Stamping in Manufacturing
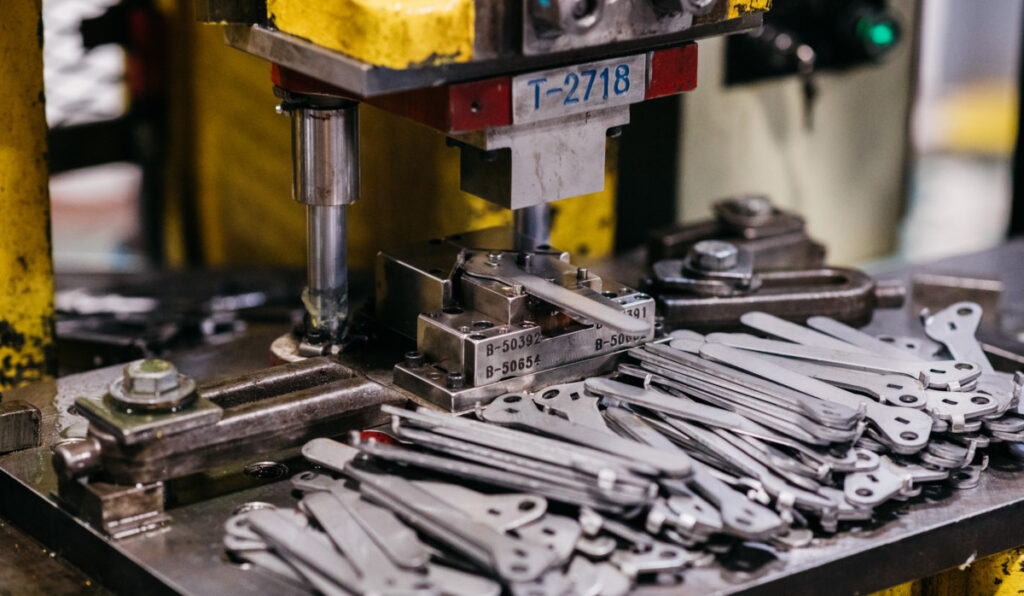
Cost-efficiency
One of the major benefits of metal stamping is its cost-effectiveness, especially when producing parts at a large scale. Due to its bulk manufacturing capabilities, the per-piece cost is significantly reduced, providing substantial savings for businesses.
Precision
Metal stamping is renowned for its precision. The use of specialized dyes and tools ensures that each part is consistent and meets exact specifications, ensuring repeatability in production and minimizing errors.
Versatility
The adaptability of metal stamping is another strong point. It can be applied to a wide range of metals and alloys, allowing manufacturers to select the most suitable material for their specific needs, be it strength, durability, or aesthetic appeal.
Speed
In comparison to many alternative manufacturing methods, metal stamping stands out for its rapid production times. This efficiency not only means quicker turnarounds for orders, but also contributes to increased overall productivity.
Key Applications and Industries of Metal Stamping

Automotive
Metal stamping is indispensable in the automotive sector. It’s used to produce essential parts such as brackets, hangers, and shields, which contribute to both the structural integrity and functionality of vehicles.
Electronics
In the realm of electronics, metal stamping facilitates the production of connectors, terminals, and springs – components necessary for the assembly and operation of electronic devices.
Aerospace
Given the stringent standards of the aerospace industry, the precision offered by metal stamping is invaluable. It aids in crafting exacting components for aircraft, ensuring safety and performance in the skies.
Medical
The medical field relies heavily on the precision and reliability of metal stamped products. Surgical tools and implantable devices for patient care and surgical procedures, are often the fruits of this manufacturing process.
Jewelry
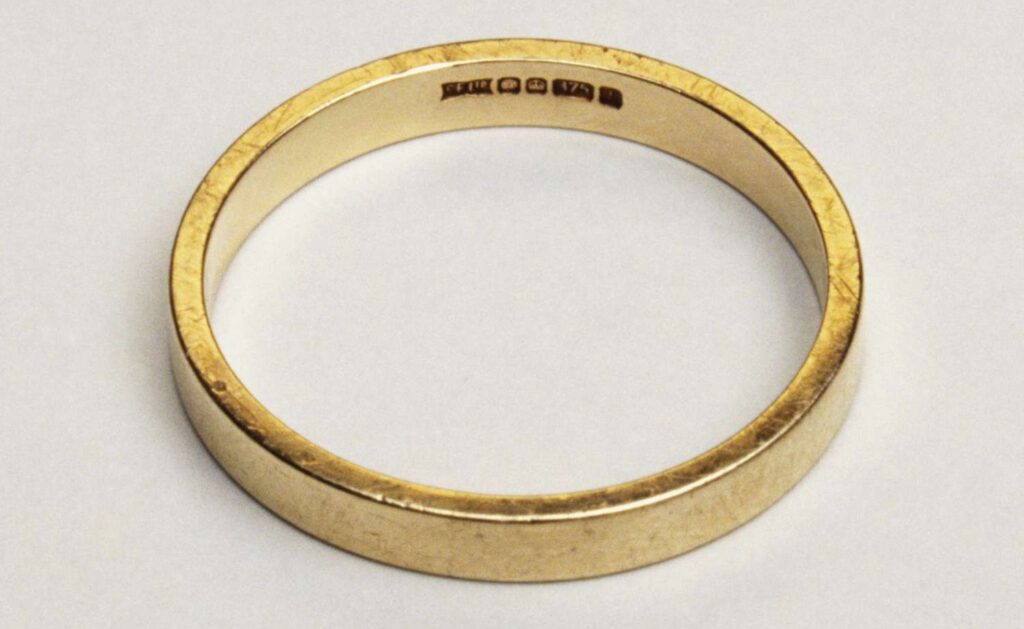
In the world of jewelry, it’s utilized for intricate detailing and hallmarking, adding value and authenticity to each piece.
Technological Innovations in Metal Stamping
Over the years, metal stamping has witnessed significant technological evolution, primarily driven by the relentless pursuit of efficiency and precision in manufacturing.
One of the most notable advancements is in stamping press technology. Modern presses are not only faster but also more energy-efficient, enabling manufacturers to produce more while consuming less.
These presses come with sophisticated control systems, allowing for better regulation of pressure and precision, ensuring that each stamped piece is consistent in quality and dimensions.
In tandem with advanced press technologies, the incorporation of robotics and automation has revolutionized the metal stamping process. Automated arms and machines can handle metals with greater accuracy, reducing human error and increasing production speed.
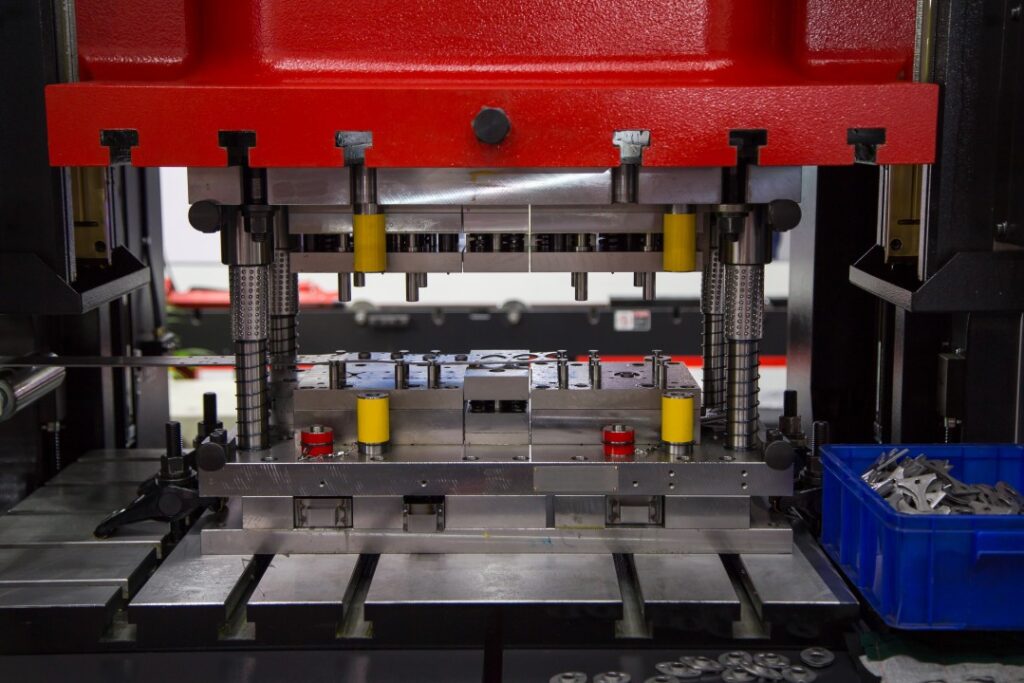
Hybrid stamping techniques, which combine traditional methods with newer processes, have emerged, offering manufacturers more flexibility and capabilities than ever before. Furthermore, the integration of Artificial Intelligence (AI) is ushering in an era of predictive maintenance.
By analyzing machine data and identifying patterns, AI can predict when a piece of equipment is likely to fail or require maintenance, thus minimizing downtime and ensuring seamless production.
The convergence of these technologies promises a future for metal stamping that is not only more efficient but also more adaptable to the ever-evolving demands of the manufacturing industry.
Metal stamping stands as a testament to the confluence of tradition and technology in the manufacturing realm. As we’ve journeyed through its many applications, technological advancements, and its role across various sectors, it’s evident that this process remains pivotal in shaping modern industries.
With its evolving techniques and the promise of further innovation, metal stamping is poised to continue its legacy of precision and efficiency for years to come.
You can also read our guide on setting up your manufacturing business and learn something new along the way.