From Pixels To Patterns: The Art And Science Of Digital Fabric Printing
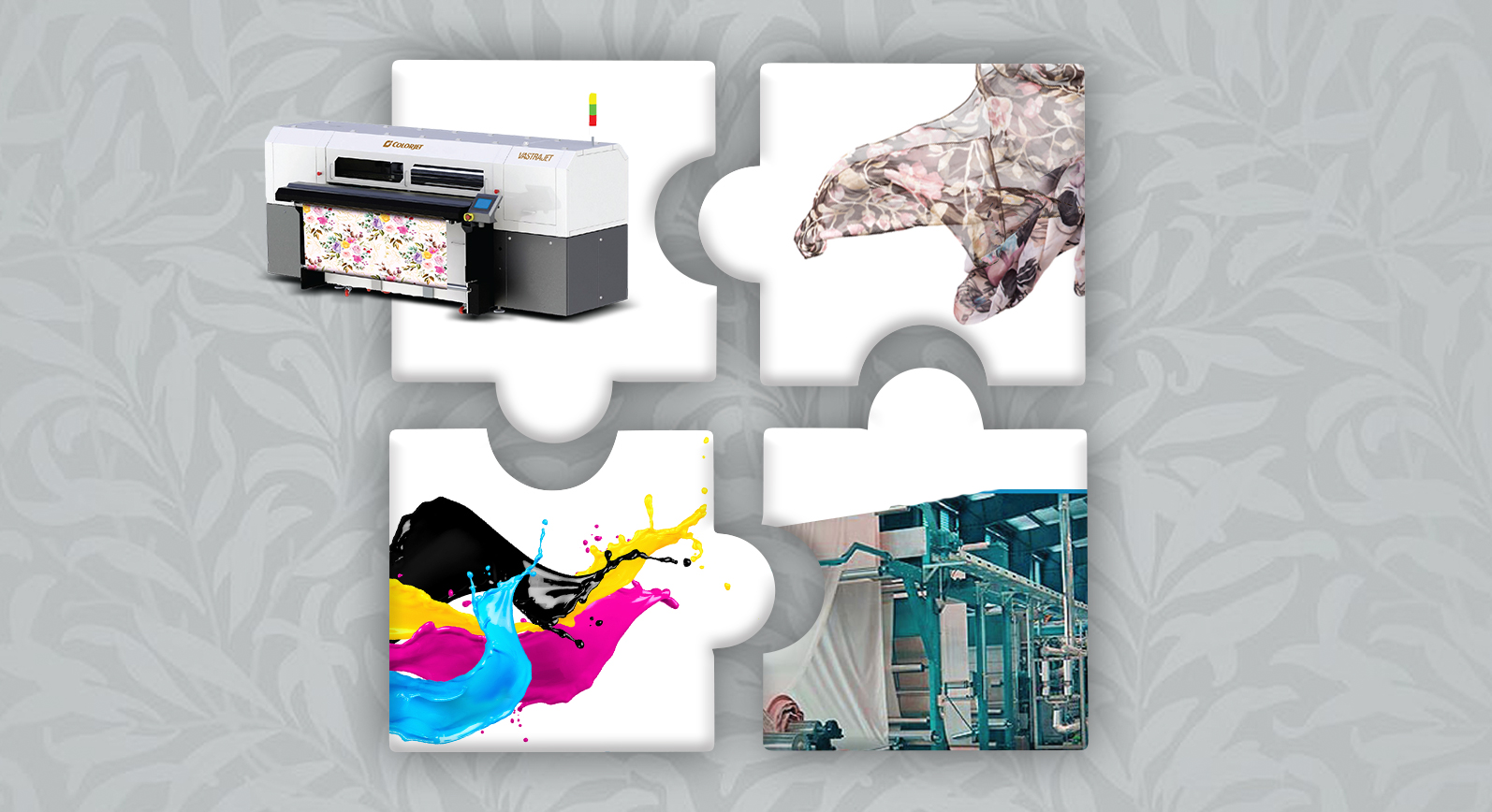
The textile industry has been revolutionized by digital fabric printing, which combines the creativity of design with the technical principles of inkjet printing. Designers and artists may accurately implement their ideas by using cutting-edge techniques.
The art and science of digital fabric printing have opened up new vistas for creativity and personalization, from conceptualizing designs to comprehending color management and ink compositions.
This article will delve into the artistry and technology that go into this ground-breaking technique as we explore the fascinating world of digital fabric printing in this article.
The Evolution Of Fabric Printing
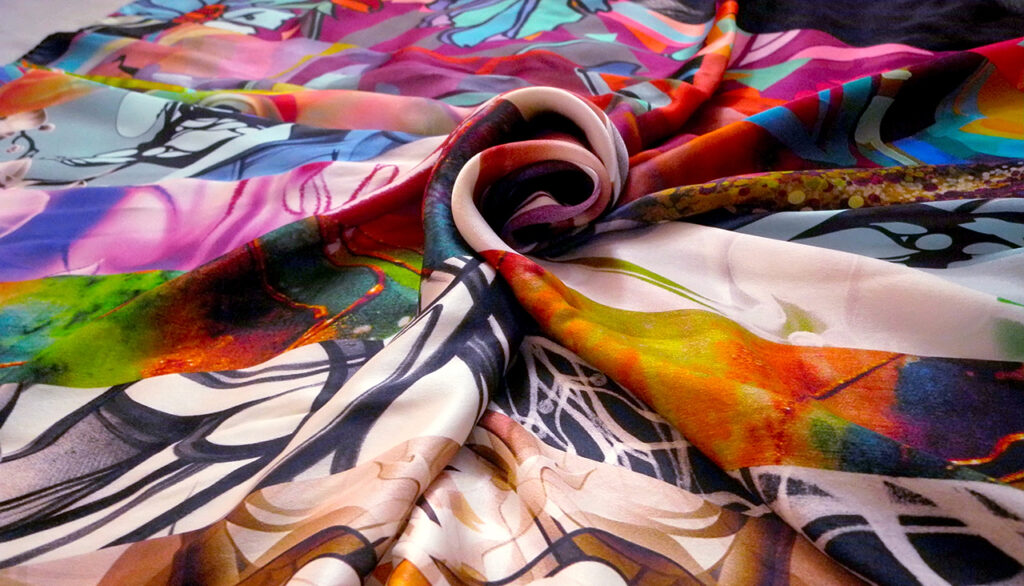
The old skill of fabric printing has developed over time. This age-old practice is changing to adapt to new technologies and artistic trends, starting with the oldest methods of hand-stamping and block printing and continuing with the introduction of digital fabric printing.
1. Origins Of Fabric Printing
Ancient civilizations such as Egypt, India, and China are the origins of fabric printing for thousands of years. These ancient societies decorated textiles in several ways, including hand painting, block printing, and resist dyeing. Fabric printing served as a medium for symbolism, cultural identity, and social rank in these prehistoric communities in addition to serving as an ornament.
2. The Age Of Industrialization
In the 18th and 19th centuries, the Industrial Revolution led to significant advancements in printing and fabric manufacturing. The development of automated procedures, such as the roller printing machine, allowed printed textiles to be produced in large quantities. It was a watershed moment in the development of fabric printing because it allowed more people to afford attractive fabrics.
3. Screen Printing And The Modern Era
In the 20th century, screen printing became the predominant method, revolutionizing cloth printing. This technique entailed printing vivid and intricate designs on the fabric by transferring ink through a mesh screen. Flexibility is afforded by screen printing, which allows complex patterns and various colors.
The Art Of Digital Fabric Printing
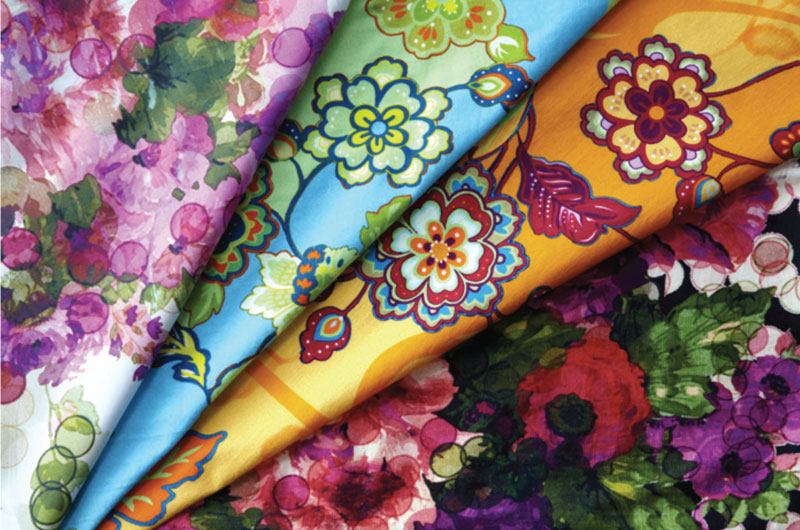
Digital fabric printing enables designers and artists to express their creativity and realize their visions with unmatched accuracy and detail on fabric. Digital fabric printing has revolutionized the textile business by fusing technology and creativity and opening new channels for expression and innovation.
1. Designing Patterns For Digital Fabric Printing
A skillful fusion of technical knowledge, imagination, and expertise goes into creating patterns for digital fabric printing. Artists and designers can form complex and captivating designs that transcend the limitations of traditional printing methods.
Several crucial elements of the design process are listed below:
a. Conceptualization
It begins with conceptualizing a design idea, whether it is motivated by nature, culture, a personal tale, or an abstract idea. To develop a visual narrative that translates into the fabric, artists experiment with several topics, patterns, and color schemes.
b. Digital Tools And Software
Digital design software, such as Adobe Photoshop or Illustrator, is a major component in digital fabric printing. Artists may convert their ideas into digital files that they can then alter to get the required effects with shapes, colors, and textures.
c. Pattern Repeat And Scaling
The design is chosen so that it repeats naturally over the fabric and keeps its integrity at different scales. Artists work continuously on their designs to get a balanced and aesthetically acceptable product.
2. Exploring Texture And Detail
The capacity to include complex textures and minute details in the designs is one of the fascinating features of digital fabric printing. The visual experience is improved by the haptic, layered, and depth illusions that artists can produce. They may capture fine details and textures that give the printed fabric more depth and richness by altering pixels and using high-resolution data.
3. Customization And Personalization
Customization and personalization are possible with digital fabric printing, allowing designers and artists to produce one-of-a-kind items that speak to specific people. Digital printing provides the freedom to respond to unique preferences and interests, whether it is customizing patterns, including personal touches, or including personalized messaging. The fabric gains value and an emotional connection through this personalized method, increasing its significance for the end consumers.
The Science Of Digital Fabric Printing
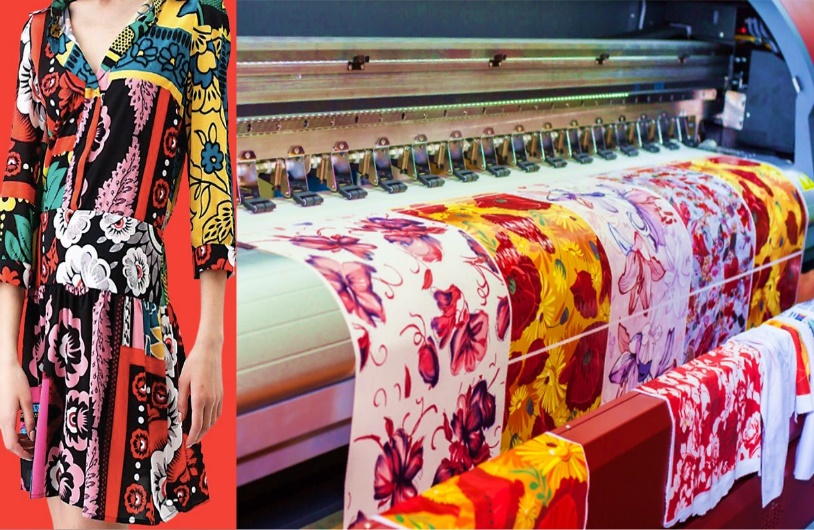
Digital fabric printing revolutionizes the textile business by effortlessly fusing art and technology. Detailed reproduction is made possible by a technological procedure that is hidden behind the vivid and elaborate designs that adorn materials.
1. Inkjet Printing Technology
Digital fabric printing relies heavily on inkjet printing technology. Micron-sized nozzles used by inkjet printers spray the ink onto fabric to produce the required patterns. Before being released in droplets, the ink is carefully regulated and applied to the fabric’s surface. The fundamental principles consist of :
a. Droplet Formation
Inkjet printers use thermal or piezoelectric technologies to form droplets. In piezoelectric printheads, a piezoelectric crystal receives an electric charge that vibrates and releases ink droplets. Thermal printheads heat the ink with the help of tiny heating elements, creating bubbles that push the droplets of ink onto the fabric.
b. Drop-On-Demand Technology
The drop-on-demand theory of inkjet printing states that droplets form when required. By accurately controlling droplet size and positioning while reducing ink loss, it produces highly detailed prints.
2. Colorant And Ink Formulations
It takes science to create the colorants and inks which are used in digital fabric printing. Viscosity, surface tension, colorfastness, lightfastness, and washability should be considered while forming the ink. Modern research and development are used to increase ink formulas, resulting in solutions with improved color accuracy, longevity, and environmental friendliness.
3. Pretreatment And Post-Treatment Processes
To maximize ink absorption, color brightness, and durability during digital fabric printing, pretreatment, and post-treatment procedures are used. Pretreatment of the cloth frequently requires the application of specialized chemicals to enhance ink penetration and fixation. Post-treatment processes may involve heat setting or steam fixing to improve colorfastness.
Future Directions In Digital Fabric Printing
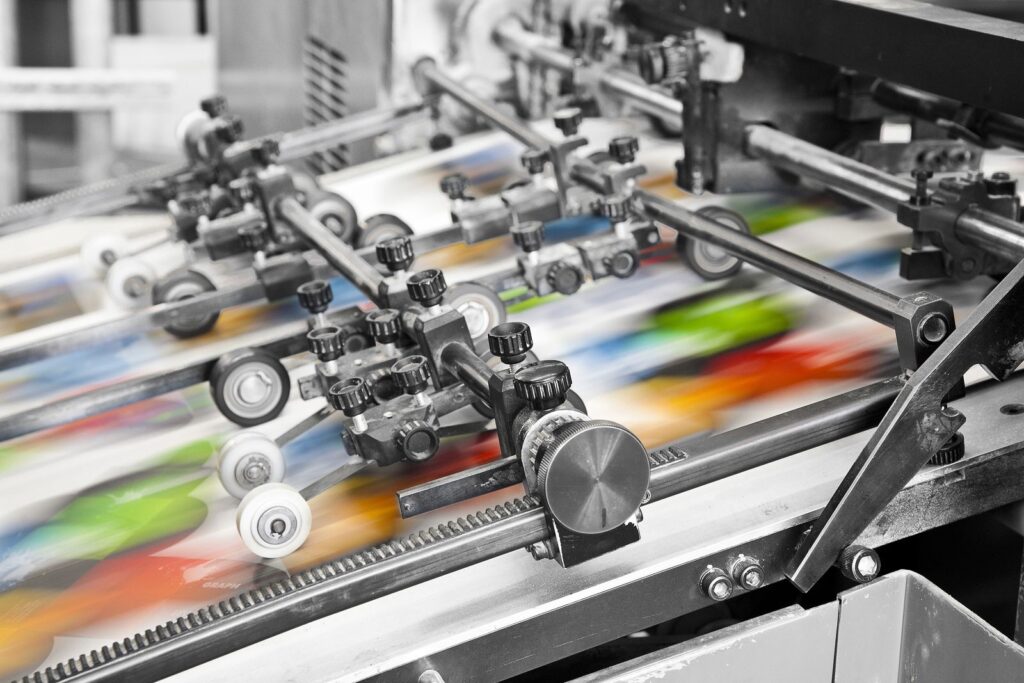
Exciting possibilities lie in the future of digital fabric printing. Key developments and trends include:
1. Integration Of Artificial Intelligence (AI) And Machine Learning
The design process is automated, color management is optimized, and print quality is improved by the use of AI and machine learning algorithms. They can identify patterns, suggest design modifications, and boost output effectiveness.
2. Smart Textiles And Wearables
Digital fabric printing can make it easier to incorporate technology into textiles as conductive inks and electronic components improve. It creates opportunities for wearable electronics, smart textiles, and interactive fabric surfaces.
3. Sustainability And Eco-Friendly Practices
The textile sector is paying more and more attention to environmental responsibility. Utilizing recyclable materials, natural dyes, and waterless printing techniques may be future developments in digital fabric printing.
Conclusion:
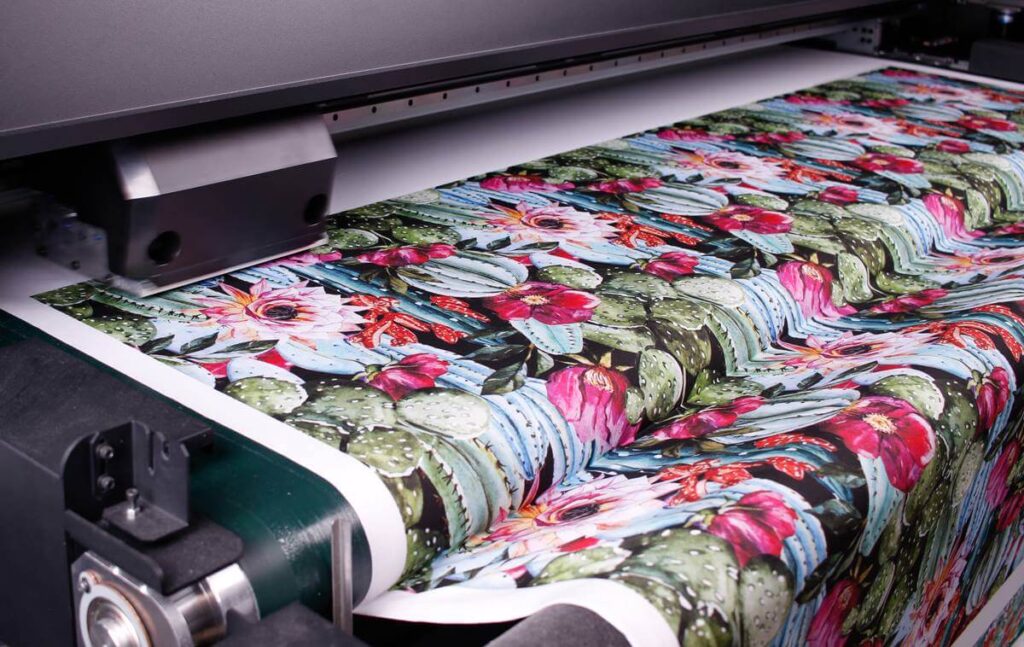
In conclusion, digital fabric printing integrates artistic design with technical inkjet printing principles, color blending, ink formulas, and pretreatment/post-treatment methods. This method has completely transformed the textile business with its creative potential and customized options.
Digital fabric printing will continue to influence textile design and production in the future as technology develops, enabling creative expression while keeping fine control over the printing process for designers and artists. Digital fabric printing has ushered in a new era of textile innovation and sustainability by fusing art and science.