Choosing the Right Sheet Metal Gauge: A Comprehensive Guide for Fabricators
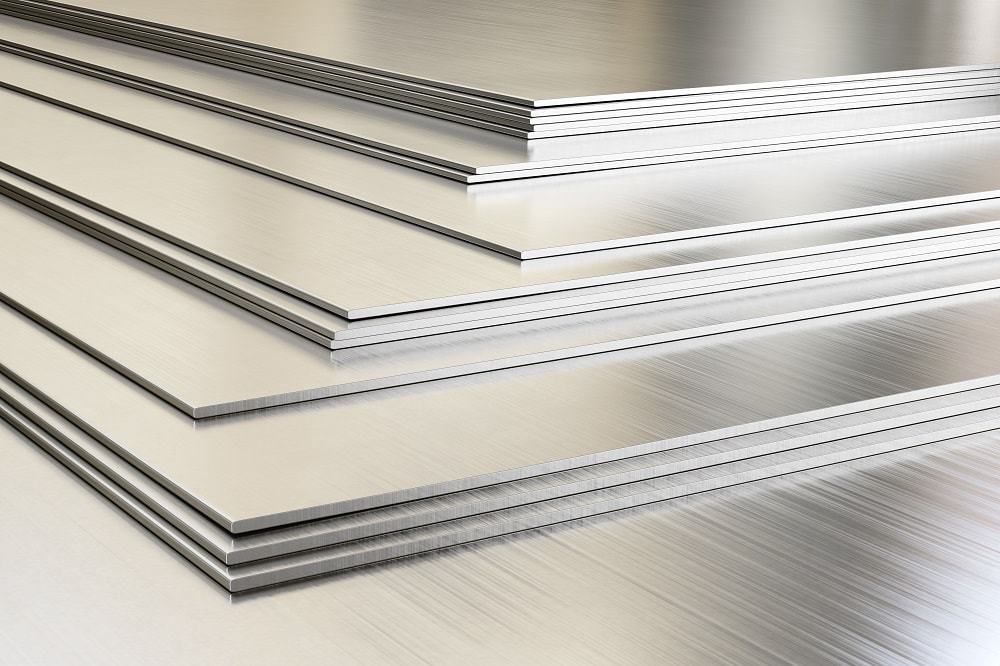
Sheet metal is a versatile and durable material that is used in a wide range of industries, from construction to manufacturing. As a fabricator, choosing the right sheet metal gauge for your project is essential to ensure the structural integrity and performance of your product.
What is Sheet Metal Gauge?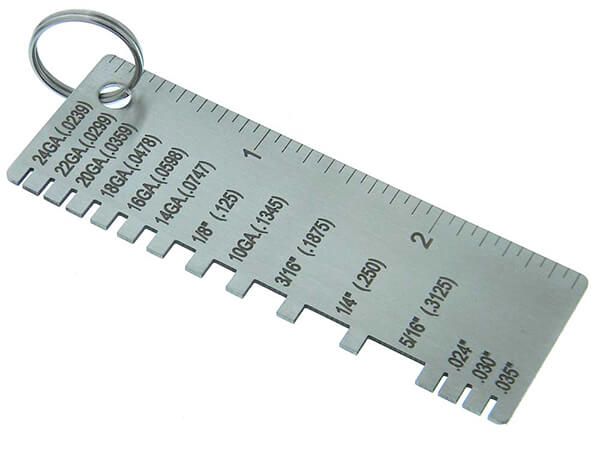
A sheet metal gauge is a numerical representation of the thickness of metal. It is expressed in terms of a gauge number, with higher numbers indicating thinner sheet metal. The standard system used in the United States ranges from 7 to 30, with 7 being the thickest and 30 being the thinnest.
Tips for Choosing the Right Gauge
1. Consider the Material
Different materials have different properties and require different gauges to achieve the desired strength and durability. Before selecting it, consider the material you will be using and its properties. If you are unsure, consult with a supplier or a materials engineer to help you choose the right one.
2. Determine the Application
The intended use of sheet metal is a critical factor that influences the choice of gauge. Consider the loads and stresses the sheet metal will encounter in its application, as well as the environmental conditions, such as temperature and humidity. This information will help you select the one that can withstand these factors.
3. Factor in Manufacturing Processes

The manufacturing process used for the sheet metal also influences the gauge choice. Certain processes, such as stamping and forming, require a specific minimum thickness to prevent deformation or tearing. Make sure you understand the requirements of the manufacturing process.
4. Look at Industry Standards
Many industries have established standards for sheet metal gauges based on the materials used and the intended application. These standards provide guidance on the appropriate gauges for specific applications and can be a useful reference.
5. Test and Validate
Once you have selected a gauge, it is essential to test and validate its performance. Conducting tests on the sheet metal, such as tensile strength and bend tests, can help you ensure that it meets the required standards and specifications.
In addition to the tips provided, it is essential to understand the relationship between sheet metal gauge and cost. Generally, the thicker the gauge, the more expensive the metal. Therefore, it is essential to strike a balance between the required strength and durability and the cost of it.
It is also worth noting that certain industries, such as the automotive and aerospace industries, have specific requirements for sheet metal gauges. These requirements are often based on safety standards and regulations, and failure to comply with them can result in severe consequences, such as product recalls and legal action. Therefore, it is essential to understand the industry-specific requirements and comply with them.
Why Should You Consider Laser Cut Metal Gauges?
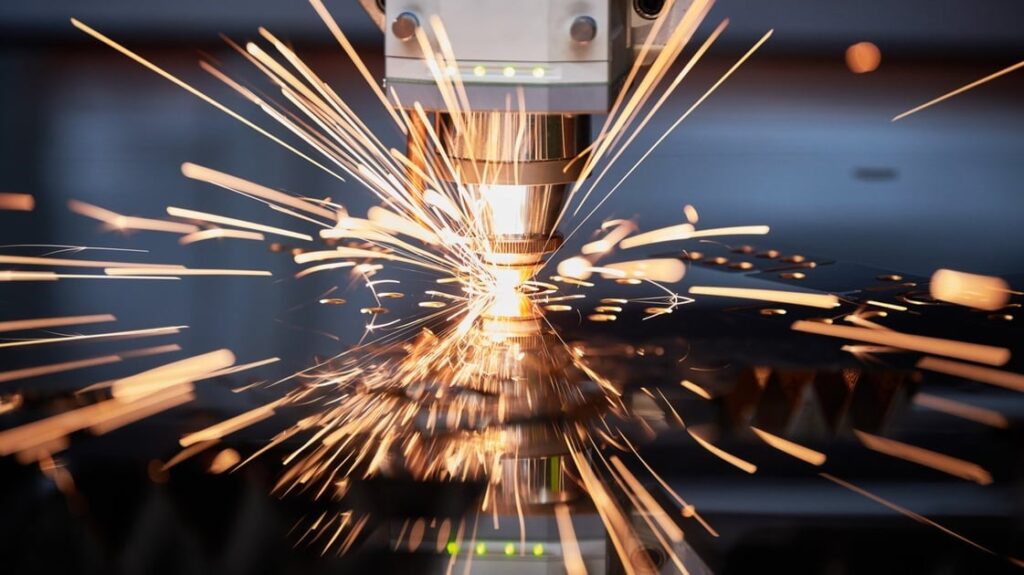
Laser-cut metal gauge offers a range of advantages that make it a compelling option for various
applications. Here are several reasons why you should consider using laser-cut metal gauge:
Precision:
Laser cutting technology provides exceptional precision and accuracy. The focused laser beam creates clean, precise cuts with tight tolerances, ensuring that the final product meets your exact specifications. This precision is crucial, especially for intricate designs or projects that require fine details.
Versatility:
Laser-cut metal gauge is highly versatile and can be used to cut a wide range of materials, including stainless steel, aluminum, brass, and more. Whether you need thin or thick gauge metals, laser cutting can accommodate various thicknesses, making it suitable for a diverse range of applications.
Complex Designs:
This form of cutting allows for the creation of intricate and complex designs that would be challenging to achieve with other cutting methods. The laser beam follows a computer-programmed pattern, enabling the precise cutting of intricate shapes, patterns, or even text.
Clean Edges:
Laser cutting produces clean, smooth edges without burrs or roughness, reducing the need for additional finishing or processing. The high precision of the laser beam results in sharp and crisp edges, enhancing the overall aesthetic appeal of the final product.
Minimal Material Waste:
Laser cutting maximizes material utilization, minimizing waste and reducing costs. The focused laser beam precisely cuts the desired shapes, optimizing the use of the material and minimizing scrap.
Conclusion
Choosing the right gauge is a critical step in the fabrication process. It requires consideration of several factors, including the material, application, and manufacturing process.
By following the tips outlined in this guide, you can make an informed decision on the appropriate gauge for your project. Remember to consult with experts, conduct tests, and validate the performance of the sheet metal to ensure that it meets the required standards and specifications.